Double Injection Molding (also known as two-shot molding or overmolding) is an advanced plastic processing technology that involves injecting two different materials or colors of plastic in a single production cycle to create composite-structured products. This technique is widely used in industries such as consumer electronics, automotive components, and medical devices, and is highly regarded for its efficiency, design flexibility, and superior product performance. This article explores the core advantages and applicable scenarios of double injection molding.
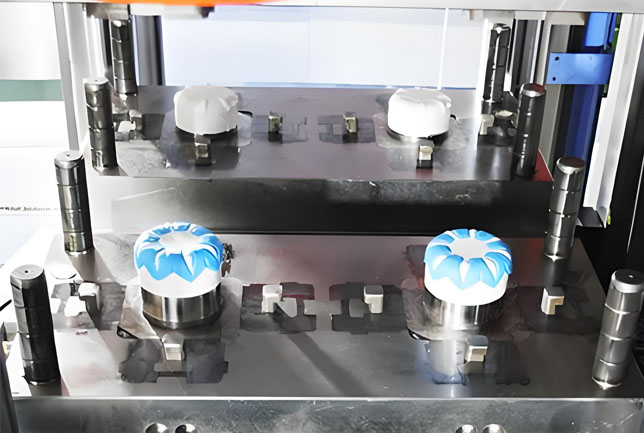
Advantages of Double Injection Molding
1. Improved Production Efficiency and Cost Reduction
Double injection molding completes two injections in one mold, eliminating the additional steps and time required for traditional multi-component assembly. By avoiding extra assembly processes, companies can significantly reduce labor costs and production cycles, enhancing overall efficiency.
2. Enhanced Functionality and Aesthetics
Material combination for optimized performance: For example, combining soft materials (TPU, TPE) with rigid materials (ABS, PC) can improve slip resistance, shock absorption, and tactile feel.
Dual-color or multi-color designs: Complex color combinations can be achieved without post-processing steps like painting or bonding, elevating the product’s visual appeal.
3. Improved Sealing and Durability
Double injection molding enables molecular-level bonding between two materials, reducing gaps that may occur with traditional adhesive or insert molding. This enhances waterproofing (e.g., in waterproof switches or seals) and long-term durability.
4. Reduced Waste and Environmental Benefits
Since no additional adhesives or assembly materials are needed, double injection molding minimizes waste generation. Additionally, some processes can incorporate recycled materials as inner layers, aligning with sustainability trends.
5. Greater Design Freedom
Engineers can integrate multiple functionalities into a single component, such as localized soft-touch areas or combinations of transparent and opaque sections (e.g., LED lamp covers), meeting complex product requirements.
Applicability of Double Injection Molding
1. Consumer Electronics
Phone cases (hard outer shell for scratch resistance + soft inner layer for shock absorption)
Buttons (dual-color legends, wear-resistant)
Wearable devices (waterproof sealing structures)
2. Automotive Industry
Steering wheels (rigid core + non-slip soft coating)
Light assemblies (integrated transparent and opaque sections)
Interior trim (decorative dual-color effects)
3. Medical Devices
Surgical instrument handles (non-slip soft grip + sterilizable hard plastic)
Sealed containers (leak-proof structures)
4. Household and Daily-Use Products
Toothbrushes (rigid handle + soft-grip coating)
Kitchenware (heat-resistant + anti-scald material combinations)
Double injection molding technology, with its notable advantages in efficiency, versatility, and environmental friendliness, has become an indispensable advanced manufacturing method in modern industry. By combining two materials or colors in a single production cycle, this technology not only significantly improves production efficiency and reduces costs but also enhances product functionality, aesthetics, and durability. Its applications span a wide range of fields, including consumer electronics, automotive, medical devices, and household goods, meeting complex design requirements and high-performance standards. Additionally, if you have the manufacturing requirements, please contact us.