With the surging demand for high-performance silicone products in industries such as medical, automotive, and consumer electronics, Liquid Silicone Rubber (LSR) injection molding technology has emerged as a manufacturing favorite due to its efficiency, precision, and superior material properties. This article provides an in-depth analysis of the LSR injection molding process, product characteristics, and its broad application prospects.
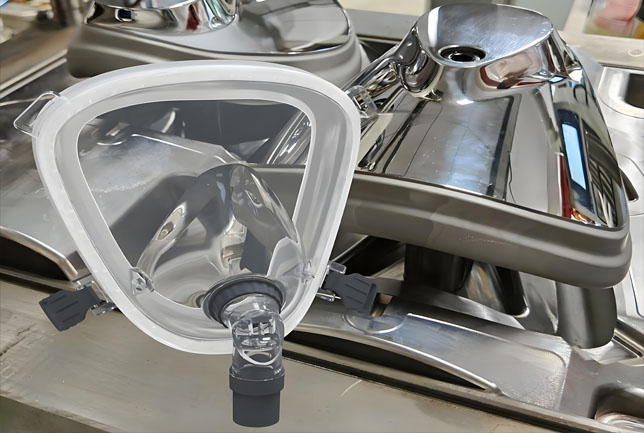
I. LSR Injection Molding: A Highly Efficient and Precise Manufacturing Process
Liquid Silicone Rubber (LSR) injection molding is an advanced processing technology primarily used to produce high-precision, elastic silicone products. The core process includes:
1. Material Mixing & Degassing
LSR is typically stored as a two-component system (A/B parts). Before production, the components are precisely mixed and degassed under vacuum to eliminate air bubbles, ensuring product quality.
2. Cold Runner Injection Molding
Dedicated LSR injection machines are equipped with cold runner systems to prevent premature curing. The mixed LSR is injected into high-temperature molds (150–200°C), where it vulcanizes rapidly within seconds to minutes.
3. Post-Curing & Surface Treatment
Some products undergo secondary vulcanization to enhance performance or receive surface treatments (e.g., coating, printing) to meet specific application requirements.
The key advantages of LSR injection molding lie in its high automation and precision-forming capabilities, making it ideal for complex structures and mass production.
II. Exceptional Properties of LSR Products
LSR injection-molded products exhibit irreplaceable advantages across multiple industries:
1. Extreme Temperature Resistance
Operating range: -50°C to 250°C, with short-term tolerance exceeding 300°C—ideal for automotive engine components, high-temperature cookware, etc.
2. Biocompatibility & Safety
Widely used in medical applications (e.g., baby bottle nipples, surgical instrument seals).
3. High Elasticity & Durability
Excellent fatigue resistance, suitable for reusable seals, buttons, and similar products.
4. Precision Molding Capability
Capable of producing micron-level precision parts (e.g., optical gaskets, micro-seals) with tolerances as tight as ±0.05mm.
5. Eco-Friendliness & Aesthetics
Recyclable material with customizable colors to meet diverse design needs.
III. Broad Applications & Market Potential
LSR injection molding technology has penetrated multiple high-end manufacturing sectors:
Healthcare: Artificial organ components, respiratory masks, medical catheters.
Automotive: EV battery seals, waterproof lamp gaskets, sensor housings.
Consumer Electronics: Smartwatch waterproofing, touch-sensitive buttons.
Infant Products: Bottle nipples, teething toys (non-toxic, withstands sterilization).
Industry data indicates the global LSR market is projected to exceed $2.5 billion by 2025, with a CAGR of over 8%, driven primarily by medical and automotive demand.
IV. LSR vs. Traditional Solid Silicone (HTV): A Technical Comparison
- | Feature | LSR Injection Molding | Traditional HTV Silicone |
- | Production Efficiency | Seconds-level curing, suited for mass production | Longer curing time, ideal for small batches |
- | Design Complexity | Capable of ultra-thin walls & intricate geometries | Limited to simpler shapes |
- | Cost-Effectiveness | Higher mold cost but lower per-unit cost | Lower tooling cost, better for customization |
With the rapid growth of 5G, EVs, and wearable devices, LSR injection molding will play an increasingly vital role in precision sealing, flexible electronics, and biomedical applications. LSR injection molding technology is driving the silicone product industry toward higher precision and sophistication. Contact us for your LSR injection molding needs!