As industrial products increasingly demand functional integration, lightweight design, and high reliability, insert molding technology has emerged as a critical process in industries such as electronics, automotive manufacturing, and medical devices. By seamlessly combining metal or non-metal inserts with plastic in a single molding step, this technology significantly enhances product performance and production efficiency, revolutionizing modern manufacturing.
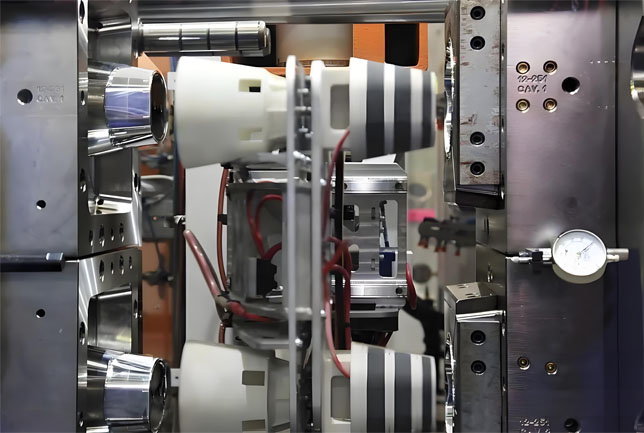
Insert Molding: A Precision Fusion Process
The core of insert molding lies in placing pre-processed inserts (e.g., metal threaded sleeves, conductive terminals, or ceramic plates) precisely into an injection mold, followed by injecting molten plastic to encapsulate and bond with the inserts. The process consists of four key steps:
1. Insert Pre-Treatment: Cleaning, sandblasting, or chemical treatments improve adhesion between inserts and plastic, while preheating may reduce thermal stress.
2. Precision Positioning: Robots or manual labor secure inserts in the mold to prevent displacement during molding.
3. Injection Molding: Under high temperature and pressure, molten plastic fills the cavity, forming a tight bond with the inserts.
4. Post-Processing & Inspection: Trimming excess material and conducting quality checks (e.g., pull tests, dimensional verification).
Broad Industrial Applications for Efficient Production
Insert molding is making a significant impact across industries:
Electronics: USB connectors, sensor housings, etc., integrate metal inserts for conductivity and structural strength.
Automotive: Transmission sensors, interior functional parts, etc., achieve lightweight and durable designs.
Medical Devices: Surgical instrument handles, disposable seals, etc., combine metal and plastic for sterility and ergonomics.
The technology’s standout advantages include reduced assembly steps, lower production costs, and enhanced functionality. For example, traditional threaded components may require secondary tapping or bolting, while insert molding completes the process in a single step, drastically improving efficiency.
Challenges and Future Trends
Despite its benefits, insert molding demands extremely high process control, where insert positioning accuracy and material bonding strength directly affect quality. The industry is addressing these challenges through high-precision mold design, automated positioning systems, and AI-driven injection parameter optimization.
Looking ahead, advancements like multi-material composites and 3D-printed inserts will expand applications in aerospace, wearable tech, and other high-end fields, further driving manufacturing toward greater efficiency and integration.
Insert molding is poised to lead the industry into a smarter, more integrated future, powering global industrial advancement. For custom manufacturing solutions, feel free to contact us.
Zdravo, htio sam znati vašu cijenu.