In modern manufacturing, surface treatment processes play a crucial role in determining a product’s performance, aesthetics, and durability. Painting (spray coating), anodizing, and plating are three widely used surface treatment technologies, each with distinct process characteristics, advantages, and industry applications. This article provides a detailed breakdown of these techniques, covering their process flows, product features, and industrial use cases.
1. Painting (Spray Coating): Versatile Surface Protection and Decoration
Process Flow:
Painting involves applying liquid or powder coatings to form a protective layer. Key steps include:
1. Surface Pretreatment: Substrate cleaning (degreasing, sandblasting) or chemical treatment (e.g., phosphating) to ensure coating adhesion.
2. Coating Application: Spray gun, electrostatic spraying, or dip coating to uniformly apply paints (e.g., acrylic, epoxy, polyurethane).
3. Curing: Thermal baking or UV curing to harden the coating.
Key Advantages:
– High Customizability: Wide range of colors, gloss levels (matte, glossy), and textures (metallic, stone-effect).
– Broad Substrate Compatibility: Suitable for metals, plastics, wood, and more.
– Cost-Effectiveness: Ideal for mass production with easy maintenance.
Limitations: Lower wear resistance and thermal stability; potential fading or peeling under prolonged UV exposure.
Typical Applications: Automotive bodies, home appliance casings, architectural facades, and consumer electronics.
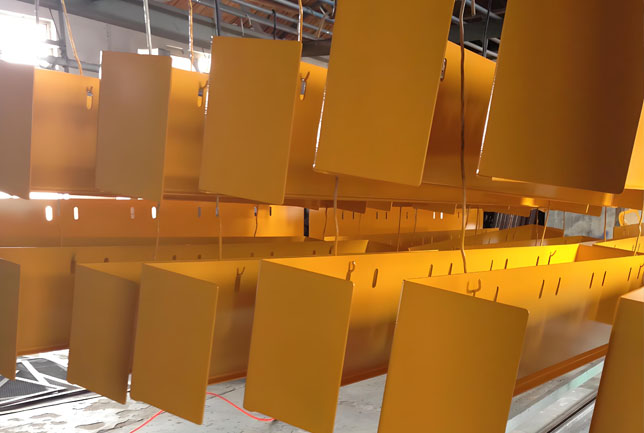
2. Anodizing: High-Performance Surface Enhancement for Light Metals
Process Flow:
Anodizing is an electrochemical process that forms an oxide layer on light metals (Al, Mg, Ti). Key steps:
1. Pretreatment: Degreasing and acid etching to remove impurities.
2. Electrolytic Oxidation: Immersion in an acidic electrolyte (e.g., sulfuric acid) with an applied current to create a porous oxide layer.
3. Sealing & Coloring: Pore sealing via hot water or chemical agents; optional dye absorption or electrolytic coloring.
Key Advantages:
– Superior Durability: High hardness, excellent abrasion/corrosion resistance, and electrical insulation.
– Lightweight: Ideal for weight-sensitive applications (e.g., aerospace, 3C products).
– Eco-Friendliness: No heavy metals; complies with RoHS standards.
Limitations: Limited to specific metals; restricted color options (e.g., black, silver, gold); oxide layer brittleness.
Typical Applications: Smartphone/laptop casings, automotive lightweight components, high-end outdoor gear.
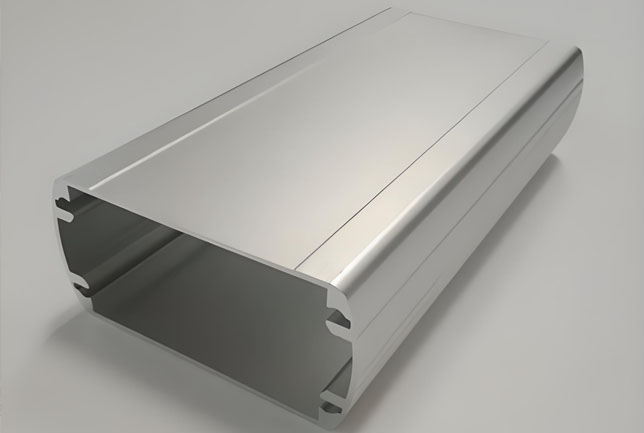
3. Plating: Functional Coatings and Premium Decorative Solutions
Process Flow:
Plating deposits a metal layer via electrolysis. Key steps:
1. Substrate Activation: Polishing and acid pickling to remove oxides.
2. Electrodeposition: Immersion in a metal-ion electrolyte (e.g., nickel, chromium, gold) with applied current to form a dense coating.
3. Post-Treatment: Polishing or passivation to enhance gloss and corrosion resistance.
Key Advantages:
– Multifunctionality:
– Decorative: Chrome/gold plating for mirror-like finishes.
– Functional: Silver/gold plating improves conductivity; hard chromium plating boosts wear resistance.
– Wide Substrate Adaptability: Primarily metals; some plastics via electroless plating.
Limitations: Complex process; some electrolytes contain cyanides (strict environmental controls required); higher costs.
Typical Applications: Automotive chrome trims, electrical connectors, jewelry, and industrial molds.
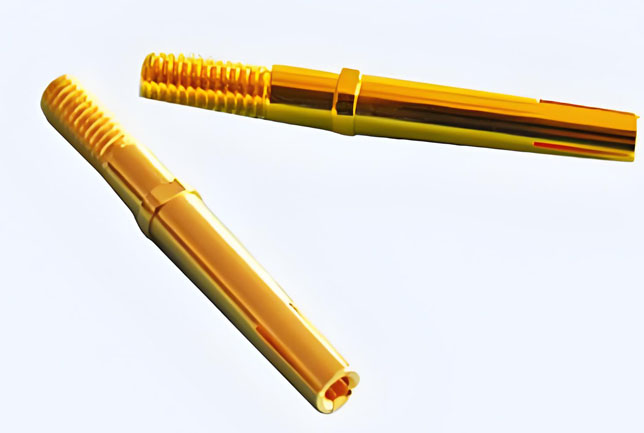
Selection Recommendations:
– Cost + Aesthetics → Painting.
– Lightweight + Durability → Anodizing.
– Conductivity/High Gloss → Plating.
The choice of surface treatment directly impacts product competitiveness. With advancements in materials and green manufacturing, these technologies will continue to innovate, delivering more efficient solutions for industry. And welcome to inquire.