Many people know that some people will also deal with the problem of poor fuel injection of aluminum alloy casing, but when you solve the problem, how long it takes and how many defects occur, but it is very different. Some took two hours to find and solve the problem, while others took a whole day to find the problem, why? The fundamental reason is that there is no systematic analysis of the poor fuel injection phenomenon and no summary of the ultimate root cause. Therefore, it is very important to be familiar with the causes of poor system control. Prosucces-metal specializes in customizing aluminum alloy casings and has rich experience in fuel injection technology. Here, the editor will talk about it.
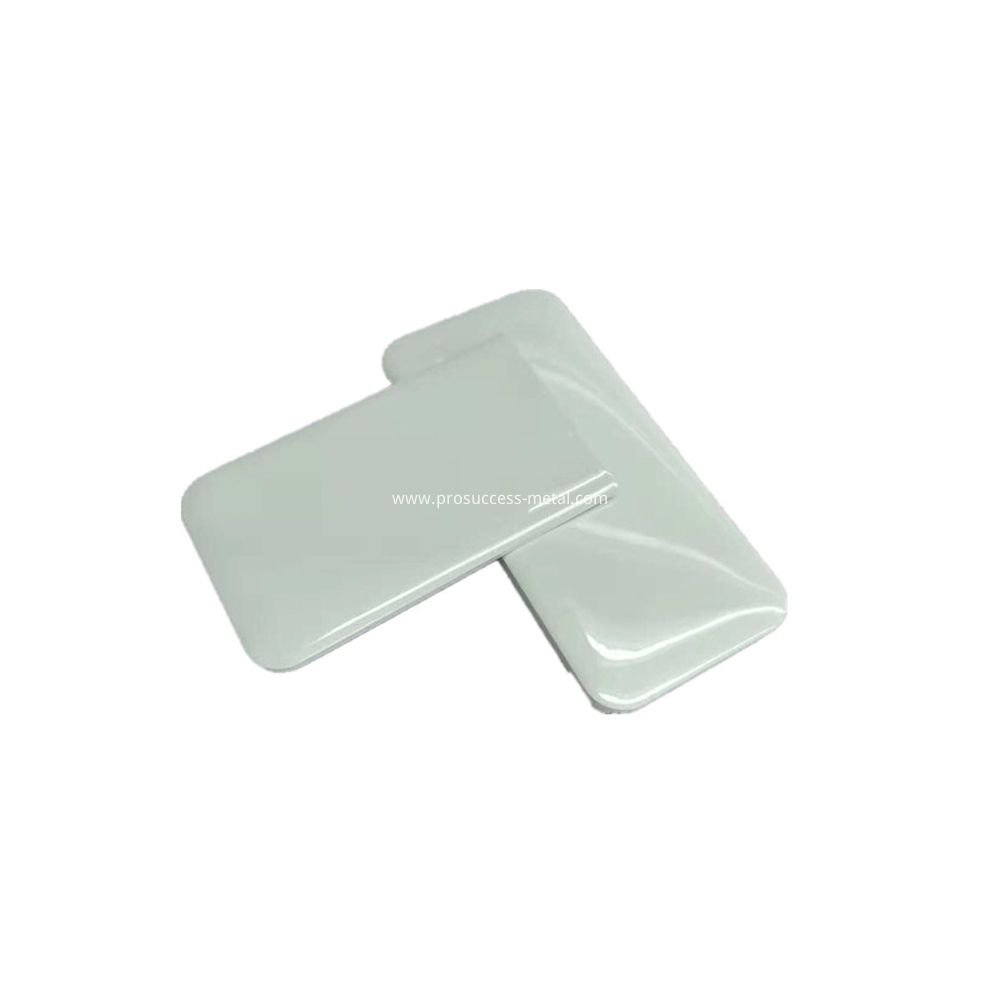
First: Less oil
Description of the bad phenomenon: The thickness of the paint film does not reach the specified thickness, exposing the true color of the aluminum alloy shell. Causes: (1) Uneven spraying caused by blockage of the fuel injection gun and unstable air pressure; (2) The spraying position of the fuel injection gun is not suitable; (3) The fixture and equipment are not properly matched with the product; (4) The fixture is poorly made, Block the spray surface.
Second: Oil accumulation
Description of the bad phenomenon: After the fuel injection, too much paint accumulates on some parts of the surface of the aluminum alloy casing, which makes the oil surface uneven. Causes: (1) The surface of the incoming material is too flat and not enough; (2) The fuel injection is too thick; (3) The fixture is not level enough; (4) The fuel injection part of the fuel gun is stable.
Third: Scratch
Description of the bad phenomenon: The surface of the product is scratched or ground. Causes: (1) It was scratched by the equipment during the production process; (2) The scratches were artificially scratched when the fixture was lowered; (3) The packaging was not in place, and the packaging material was scratched.
Fourth: Highlights
Description of the bad phenomenon: There is a difference in the gloss and color of the aluminum alloy shell surface from other places, and it is shiny. Causes: (1) The spray gun is poorly atomized; (2) The surface of the aluminum shell is not clean and there are foreign objects; (3) The bottom oil leveling is not fully dry.
Fifth: Black print
Description of the bad phenomenon: There are dark dark lines or spots on the surface of the aluminum alloy shell that has been sprayed with oil. Causes: (1) The incoming material has been scratched; (2) The clamping surface is scratched; (3) The incoming material is dirty. (4) There are different colors on the surface of the incoming material.
Sixth: Chromatic aberration
Description of the bad phenomenon: The color of the aluminum casing after fuel injection is different from that of the sample provided by the customer. Causes: (1) The incoming paint does not match the sample paint; (2) The customer changed the aluminum alloy shell material; (3) The spraying parameters were not adjusted properly; (4) The ambient humidity and drying temperature did not meet the requirements; (5) The spraying air pressure Unstable; (6) There are foreign objects in the spraying equipment; (7) The paint mix does not match the sample.
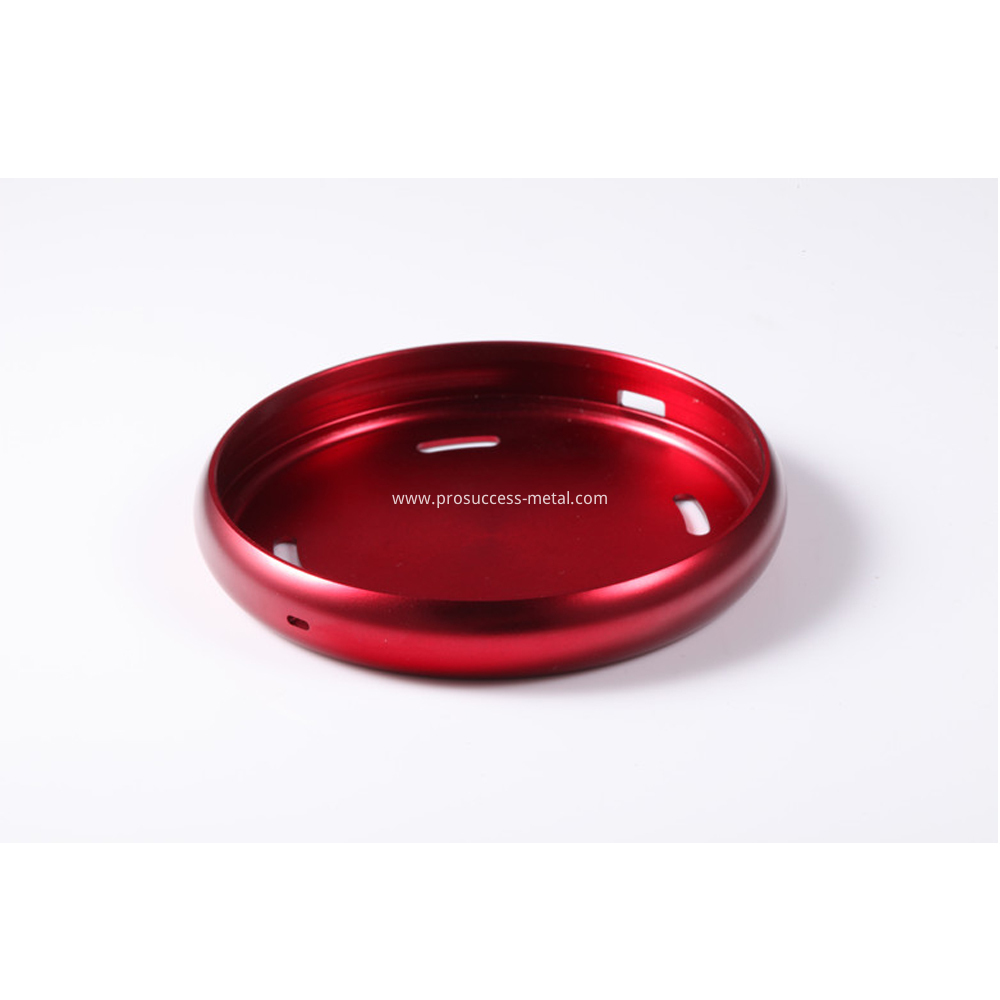
Seventh: Uneven gloss
Description of the bad phenomenon: After spraying, the surface gloss of the aluminum alloy shell is inconsistent, and there are yin and yang surfaces. Causes: (1) Uneven spraying; (2) The spray gun is unstable; (3) The paint is not stirred evenly; (4) The baking ventilation is not enough; (5) The incoming material is poor.
Eighth: Bubbles
Description of the bad phenomenon: After the aluminum shell is sprayed and dried, the surface is convex and looks like air bubbles. Causes: (1) The base oil is not dry when spraying the surface oil; (2) The baking temperature is too high; (3) The temperature rises too fast during baking; (4) There are foreign objects on the surface of the aluminum alloy casing.
Ninth: Pinhole
Description of the bad phenomenon: Needle-shaped holes appear on the surface of the aluminum shell after spraying and drying. Causes: (1) The baking temperature is too high; (2) The baking temperature rises too fast; (3) The paint solvent does not meet the requirements; (4) There are foreign objects on the surface of the product; (5) The primer is not fully dry.