In the field of plastic and composite processing, compression molding continues to play a vital role in industries such as automotive, electronics, and household appliances due to its unique process advantages and product characteristics. This technology is particularly suitable for thermosetting materials and high-fiber-content composites, offering manufacturers a cost-efficient forming solution.
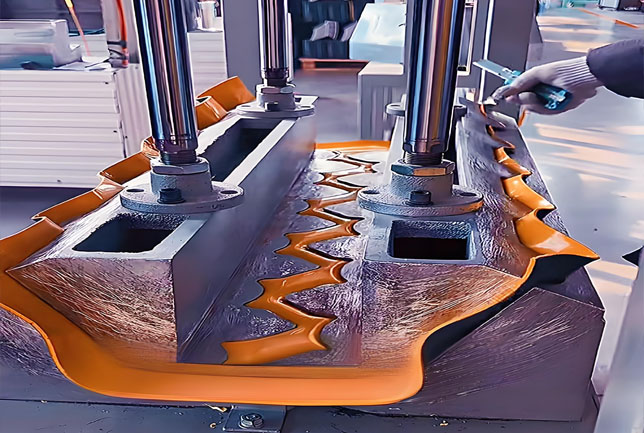
Process Principles and Workflow
The core of compression molding lies in material curing under high temperature and pressure, with the following key steps:
1. Material Preheating: Plastic powder, pellets, or preforms are heated to improve flowability.
2. Loading and Mold Closing: The material is placed into a heated mold cavity, and the mold is closed under high pressure (typically 10-50 MPa).
3. Curing and Forming:
– Thermosetting plastics (e.g., phenolic resins, epoxy resins) undergo cross-linking reactions at high temperatures (120-200°C) to form a permanently cured structure.
– Thermoplastics (e.g., PE, PP) melt and solidify upon cooling.
4. Demolding and Post-Processing: The mold is opened to remove the finished part, which may undergo trimming or surface treatment if necessary.
Key Advantages: Cost Efficiency, High Strength, and Material Versatility
Compared to injection molding or transfer molding, compression molding offers the following benefits:
– High Cost Efficiency: Simple equipment and low mold costs make it ideal for small-to-medium production runs.
– Low Internal Stress: Gradual pressure application minimizes warping, making it suitable for precision components (e.g., electrical insulators).
– Broad Material Compatibility: Capable of processing highly filled materials (e.g., glass/carbon fiber-reinforced plastics) for enhanced mechanical properties.
– Minimal Waste: No runner system, achieving material utilization rates of up to 95%.
Product Characteristics and Applications
Compression-molded products are known for their dense structure, heat resistance, and chemical durability, with key features including:
– Superior Mechanical Properties: High-pressure forming reduces internal defects, ideal for load-bearing parts.
– Excellent Dimensional Stability: Thermoset products retain shape under high temperatures (e.g., automotive under-hood components).
– High Surface Quality: Textured or smooth finishes can be molded directly, reducing secondary processing (e.g., tableware, appliance housings).
Primary Applications:
– Automotive: Brake pads, bumpers, interior parts (fiber-reinforced composites).
– Electronics: Switches, sockets, insulating components.
– Consumer Goods: Cookware handles, cutlery, buttons.
Despite longer cycle times, compression molding remains irreplaceable for high-fiber-content composites (e.g., SMC/BMC). While injection molding suits complex, thin-walled parts, compression molding excels in thick-walled, high-strength applications. Transfer molding, meanwhile, is better for intricate geometries.
As a classic forming technology, compression molding retains its relevance in modern manufacturing due to its unique cost-performance balance. If you have any product processing or customization needs in this field, please don’t hesitate to contact us!